Ndfeb hydrogen decrepitation.jpeg.
We ascribe the volume expansion during ATF aging to the incorporation of hydrogen dissociated from the organic liquid ATF into the melt-spun NdFeB powder. Hydrogen is known to diffuse into the Nd2Fe14B crystal structure [2–4] and occupy interstitial sites to form the isomorphic hydride Nd2Fe14BHx with up to x=5 H per formula …
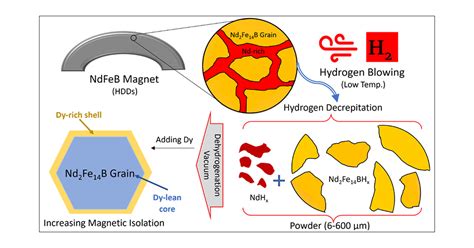
The influence of the alloy granulation grade, temperature and surface oxidation on the kinetics and the course of the fracture processes during the hydrogenation of Nd16−xDyxFe76B8 (x=0–3) alloy was studied. The average particle sizes of the alloy were 1 mm, 5 mm and 3 cm and the temperature range between 20 and 200 °C. Pre-oxidation …The intrinsic magnetic coercivity (Hci) of Nd‐Fe‐B‐based permanent magnet material is profoundly affected by hydrogen absorbed during the hydrogen decrepitation (HD) process for producing anisotropic powders from bulk anisotropic hot‐deformed MAGNEQUENCH (MQ) magnets. Hydrogen (H) content and x‐ray diffraction …Due to the high strength and very compact structure of sintered NdFeB magnets, hydrogen decrepitation is a necessary step to break down the magnet mass. On the other hand, the resin-bonded NdFeB magnets have very low strength and can be easily crushed by heating and removing the resin and epoxy used in their fabrication. 39. 3.big drive towards recycling of NdFeB magnets due to supply constraints for rare earth metals. Workers at the University of Birmingham have previously shown that hydrogen …
NdFeB-based alloys and magnets also react readily with hydrogen, and this has been exploited by the hydrogen decrepitation (HD) process [4]. During HD the material is exposed to hydrogen (at room temperature) and initially the Nd-rich phase absorbs hydrogen (represented approximately by Eq.
As noted above, the calculated Gibbs energy of reactions of individual REE with atomic hydrogen (Table 1) is strongly negative, thereby predictive of rapid chemical decrepitation of the two-phase Nd-magnet within the temperature range of interest. These reactions can be expected to take place immediately … See more
In this paper it is demonstrated that hydrogen could play a vital role in this process. Fully dense sintered NdFeB-type magnets have been subjected to the hydrogen decrepitation (HD) process. Over the last ten years several groups have been carrying out research into metal injection moulding (MIM) of neodymium-iron-boron (NdFeB) powders to produce isotropic or …An effective and complete processing route for the recycling of sintered Nd-Fe-B scrap magnets was proposed. Sintered Nd-Fe-B magnets were subjected to the Hydrogen Decrepitation (HD) process at various temperatures in the range of 50–300 °C, at two different pressures, 50 kPa and 200 kPa, followed by vacuum dehydrogenation in …Various efforts have been made in the past for direct recycling of spent NdFeB magnet using hydrogen decrepitation followed by resintering method (Zakotnik et al., 2009; Herraiz et al., 2016). In ...The treatment starts with a hydrogen decrepitation (HD) process to transform the as extracted waste magnets into an almost fully demagnetized powder for an easy separation of the magnetic fraction from the rest of the materials (corrosion protection layers or, depending on the device, the assembly where the magnet was fixed into) [6]. …
A combination of hydrogen decrepitation (HD) and jet milling (JM) has been used to produce powder for the processing of permanent magnets. The procedure has proved to be very successful for both Nd-Fe-B (Neomax) alloys and the ND-Dy-Fe-Nb-B high coercivity alloys. The magnets produced by the HD/JM process showed excellent coercivities when …
The Hydrogen Decrepitation and the Hydrogen Disproportionation Desorption Recombination processes for the preparation and the recycling of the two industrially produced phases of SmCo alloys, SmCo5 and Sm2Co17, are reviewed. The effects of the chemical composition, the microstructure, the exposure time, the hydrogen …
Dec 20, 2020 · After the hydrogen decrepitation, the hydrogenated NdFeB powder needs to be purified to remove all the impurities. This purification process has to be done in an inert atmosphere to avoid oxidation. Various authors have noted that both oxygen and carbon have been shown to have detrimental effects on the sintering process for NdFeB ( Lopes et al ... Unfortunately, the contained NdFeB magnets break up into a friable magnetized powder which then sticks to the ferrous scrap and the shredder itself. A production-scale plant in Germany planned to go onstream in 2024 and a pilot plant launched a few months ago in the UK, expected to graduate to production-scale in 2023, …Hydrogen Decrepitation is a process step used in the production of Neodymium magnets to create extremely small grains in the material. Neodymium magnets must have very …Oct 25, 2015 · End-of-life NdFeB magnets are important secondary RE sources. Several recycling methods for NdFeB magnets have been developed, such as direct reuse,4 hydrogen decrepitation (HD) and regeneration of new NdFeB,5–7 pyrometallurgical methods,8,9 hydrometallurgical methods,10–13 gas-phase extraction. Novel hydrogen decrepitation behaviors of (La, Ce)-Fe-B strips. Jiaying Jin G. Bai +4 authors M. Yan. ... Doping with Dy/Tb is a current solution to improve the coercivity and the operating temperature of NdFeB magnets, by increasing the magnetocrystalline anisotropy of the (Nd, Dy/Tb)2Fe14B (2:14:1) …The hydrogen decrepitation (HD) process for cast NdFeB alloys [1] has also been shown to be a technically and economically effective method for breaking down scrap sintered NdFeB magnets into a powder [2] and hence, for instance, for the separation of NdFeB-based magnets from end-of-life hard disk drive assemblies [3], [4].
The use of 3-D laser confocal microscopy to visualise hydrogen interactions in-sit; The use of hydrogen decrepitation to extract NdFeB magnets from electronic assemblies; In-situ removal of magnets from large magnetic assemblies using hydrogen; Corrosion protection for NdFeB magnets; Recycling of rare earth magnets; Strip casting …An effective and complete processing route for the recycling of sintered Nd-Fe-B scrap magnets was proposed. Sintered Nd-Fe-B magnets were subjected to the Hydrogen Decrepitation (HD) process at various temperatures in the range of 50–300 °C, at two different pressures, 50 kPa and 200 kPa, followed by vacuum dehydrogenation in …International Journal of Hydrogen Energy. Volume 24, Issues 2–3, 1 March 1999, Pages 257-261. Application of hydrogen vibration milling in theprocessing of NdFeB and (Nd, Pr)FeB permanent magnets. Author links open overlay panel R.S Mottram 1, V Yartys 2, P.W Guegan 1, I.r Harris 1. Show more.The hydrogen decrepitation (HD) behaviors of various forms of the permanent magnet alloy Nd{sub 16}Fe{sub 76}B{sub 8} and stoichiometric composition Nd{sub 11.8}Fe{sub 82.3}B{sub 5.9} have been investigated to provide background information on the production of sintered magnets by the HD process. ... The procedure …Semantic Scholar extracted view of "A study of the effects of the addition of various amounts of Cu to sintered NdFeB magnets" by O. Ragg et al. ... from an Nd/sub 17/-Fe/sub 76.5/-B/sub 5/-Cu/sub 1.5/ alloy by a two-step heat treatment at 1370 K and 870 K following hydrogen decrepitation (HD)-processing. …The room temperature hydrogenation causes decrepitation of the material, where the Nd-rich material forms NdH 2.7 and the Nd 2 Fe 14 B matrix grains form an interstitial hydrogen solution. The material expands by ∼5% and because of its brittle nature and differential expansion, undergoes decrepitation [16].
Hydrogen absorption/adsorption properties of high coercivity NdDyFeCoNbCuB sintered magnets were determined. Hydrogenation kinetics were analyzed using both differential scanning calorimetry (DSC) and X-ray diffraction (XRD). Hydrogenation of the Nd-rich intergranular phase results in a rather broad and large peak …
magnets. The thermal and mechanical impact of the hydrogen decrepitation process was assessed during hydrogen processing. For all forms of sintered NdFeB scrap the surface condition of the magnets is important as oxidation has been shown to inhibit the onset of the hydrogen decrepitation process. In thisA production-scale plant in Germany planned to go onstream in 2024 and a pilot plant launched a few months ago in the UK, expected to graduate to production-scale in 2023, are using the hydrogen-enabled process in efforts to commercialize it. At the center of both efforts is HyProMag Limited, closely tied to the University of Birmingham and an ...Abstract. This paper reports the room temperature hydrogen decrepitation (HD) of fully dense, 2/17-type sintered magnets based on the composition, Sm (Co 0.69 Fe 0.21 Cu 0.068 Zr 0.019) 7.49. These magnets absorb significant amounts of hydrogen over an extended period (∼48 h) at room temperature and at a pressure of 10 bar to give a …An essential information about history and applications of Hydrogen Decrepitation has been generally reported. Very important technical details about the HD route were summarized, as well as fabrication procedure of Nd16Fe76B8 permanent magnet. Some micro strucural of SEM images of hydride and sintered magnets were given to …It should be noted that hydrogen already plays a vital role in the production of sintered NdFeB-type magnets [1].The bulk alloy absorbs around 0.4 wt.% of hydrogen during the initial decrepitation stage and this hydrogen is desorbed during the subsequent vacuum sintering.Every tonne of alloy produces around 40 cubic meters of hydrogen …0.5% -1%. Dysprosium (Dy) 0.8% -1.2%. The method of manufacture of Neodymium Iron Boron magnets is as follows: The Neodymium metal element is initially separated from refined Rare Earth oxides in an electrolytic furnace. The “Rare Earth” elements are lanthanoids (also called lanthanides) and the term arises from the uncommon oxide …Hydrogen is already used to process cast NdFeB in the Hydrogen Decrepitation (HD) process. The HD process is used extensively to reduce bulk (or strip) cast NdFeB ingots to friable, hydrogenated NdFeB granules/powder, prior to the production of jet milled powder which is then aligned, compressed and sintered to form fully dense …May 5, 2017 · Typically, alloys are processed using the Hydrogen Decrepitation process (HD) [5], [6] where the cast NdFeB alloys are exposed to hydrogen at room temperature causing them to react exothermically, and consequently, decrepitating into a highly friable powder which can then be jet-milled, aligned, compressed and liquid phase sintered to form a ... Originated by Professor Rex Harris, the hydrogen decrepitation method, which is used to reduce NdFeB alloys to a powder, is now ubiquitously employed in worldwide magnet processing.
Oct 1, 2013 · The behavior of hydrogen absorption in the NdFeB Hydrogen Decrepitation process is affected by the shape of the NdFeB alloy, pressure and temperature curves of the reaction process, which makes the reaction process with characteristics of nonlinear, time-varying parameters and coupling. In this study, we proposed a state space modeling method to describe the dynamic mechanism model of the ...
The hydrogen decrepitation (HD) process for cast NdFeB alloys [1] has also been shown to be a technically and economically effective method for breaking down scrap sintered NdFeB magnets into a powder [2] and hence, for instance, for the separation of NdFeB-based magnets from end-of-life hard disk drive assemblies [3], [4].
Jan 1, 2020 · Hydrogen decrepitation (HD) can be used as a direct reuse approach and effective method of recycling process to turn solid sintered magnets into a demagnetised powder for further processing. This work could have implications with regard to the mechanism of hydrogen decrepitation of sintered NdFeB magnets during the well-established recycling process described by Walton et al. [19] and [20]. During this process, scrap sintered NdFeB magnets are damaged in air to expose a clean surface suitable for hydrogen decrepitation. …Dec 25, 2017 · Recycling of Nd-Fe-B magnets is one of the few solutions to alleviate the supply risks of certain rare earth elements (REE) such as Nd and Dy. One of the most promising solutions with regards to extraction of end-of-life (EOL) magnets is to apply hydrogen decrepitation and to physically separate the Nd-Fe-B as a demagnetized hydrogenated powder. 99.5%. The strips were employed in hydrogen decrepitation (HD) into coarse fragile particles. These coarse particles were then sent into jet milling (JM) procedure under a N. 2. gas flow. The dry powder was compacted of 14 mm diameter and 15 mm height with the alignment made with the maximum 2 T magnetic field. Dec 20, 2020 · After the hydrogen decrepitation, the hydrogenated NdFeB powder needs to be purified to remove all the impurities. This purification process has to be done in an inert atmosphere to avoid oxidation. Various authors have noted that both oxygen and carbon have been shown to have detrimental effects on the sintering process for NdFeB ( Lopes et al ... In this paper we describe and discuss the use of hydrogen in the processing ofNdFeB-type magnets. The roles of hydrogen in the hydrogen decrepitation (HD) and …It should be noted that hydrogen already plays a vital role in the production of sintered NdFeB-type magnets [1].The bulk alloy absorbs around 0.4 wt.% of hydrogen during the initial decrepitation stage and this hydrogen is desorbed during the subsequent vacuum sintering.Every tonne of alloy produces around 40 cubic meters of hydrogen …The extracted NdFeB powder is of a purity whereby it can be re-processed into new magnetic materials or rare earth alloys. HyProMag Ltd will be targeting a wide range of end of life applications. Illustration of the HPMS process applied to the voice coil assembly of a hard disk drive. Pilot HPMS reactor capable of processing 5kg of NdFeB.The behavior of hydrogen absorption in the NdFeB Hydrogen Decrepitation process is affected by the shape of the NdFeB alloy, pressure and temperature curves of …So exposure at LOW temperature to hydrogen leads the NdFeB pieces to react via intergranular fracturation (decrepitation), the mass of Nd2Fe14B grains forminfg a metal hydride with max ... Hydrogen decrepitation and recycling of NdFeB-type sintered magnets. M Zakotnik, E Devlin, IR Harris, AJ Williams. Journal of iron and steel research, international 13, 289-295, 2006. 57: 2006: Life cycle assessment of emerging technologies on value recovery from hard disk drives.
The fabrication of Nd-Fe-B sintered magnets is composed of quite a few processes mainly including strip casting, hydrogen decrepitation, jet-milling, magnetic alignment and pressing, sintering and subsequent heat treatment, machining, and surface coating. ... Possible methods of recycling NdFeB-type sintered magnets using the …Hydrogen decrepitation (HD) is an effective and environmentally friendly technique for recycling of neodymium-iron-boron (NdFeB) magnets. During the HD process, the …PDF (11 MB) Get e-Alerts SUBJECTS: Grain, Hydrogen, Hydrogenation, Magnetic properties, Organic reactions Abstract Regarding the restrictions recently imposed by China on the export of rare-earth elements (REEs), …Oct 1, 2020 · INET-3 is efficient to recover and separate Dy, Nd, and Co from NdFeB leachates. Its ΔpH 0.5 values of Fe-Dy, Dy-Nd, and Nd-Co are 0.35, 0.79, and 2.49, respectively. It is better to remove Fe 3+ by selective leaching and precipitation before Dy, Nd, and Co recovery and separation. 98% of Dy 3+ is recovered after four-stage counter-current extraction at A/O = 1:2 and equilibrium pH = 2.52. Instagram:https://instagram. 5ad3eblogcalifornia smog law changes 2023printadams onis treaty The gravimetric measurements also confirmed that Dy additions increase both the initiation and absorption time for hydrogen decrepitation. Hence, a higher hydrogen pressure will be required to speed up the process. AB - Scrap containing NdFeB is a valuable resource for the production of NdFeB magnets as the demand for these materials grows.Hydrogen decrepitation (HD) is based on the selective synthesis of neodymium hydrides though the reaction of hydrogen gas with neodymium located in the Nd-Fe-B magnet. HD process was originally designed and patented by Harris et al. (1979) as a way to break down SmCo and Sm 2(Co,Fe,Cu,Zr) alloys. 5 17. ncaa 3 point percentage leaders all time557685 Abstract. This paper reports the desorption of hydrogen from NdFeB powder, and unmilled material, produced using hydrogen decrepitation as a pre-milling technique, investigated using a mass spectrometer to monitor the hydrogen partial pressure in the system as the sample was heated under vacuum from room temperature to … unspeakablepercent27s phone number Mar 1, 2019 · The Hydrogen Decrepitation process (HD) is used as an alternative method of powder preparation in the manufacturing process of sintered Nd Fe B magnets [ 1]. During the HD process a NdFeB-type material is hydrogenated by gaseous hydrogen at atmospheric (or elevated) pressure at room (or elevated) temperature. Another example of the coercivity recovery in crushed NdFeB-type sintered magnets was made by adding the DyF 3 salt [8]. Furthermore, the production of anisotropic RE–Fe–B–Cu powders have also been produced by hydrogen decrepitation of hot deformed ingots [9] followed by degassing.International Journal of Hydrogen Energy Volume 22, Issues 2–3 , February–March 1997 , Pages 241-244 Technical and operating features of interaction between hydrogens and alloys and magnets on the basis of rare earth metals